What are glasses made of?
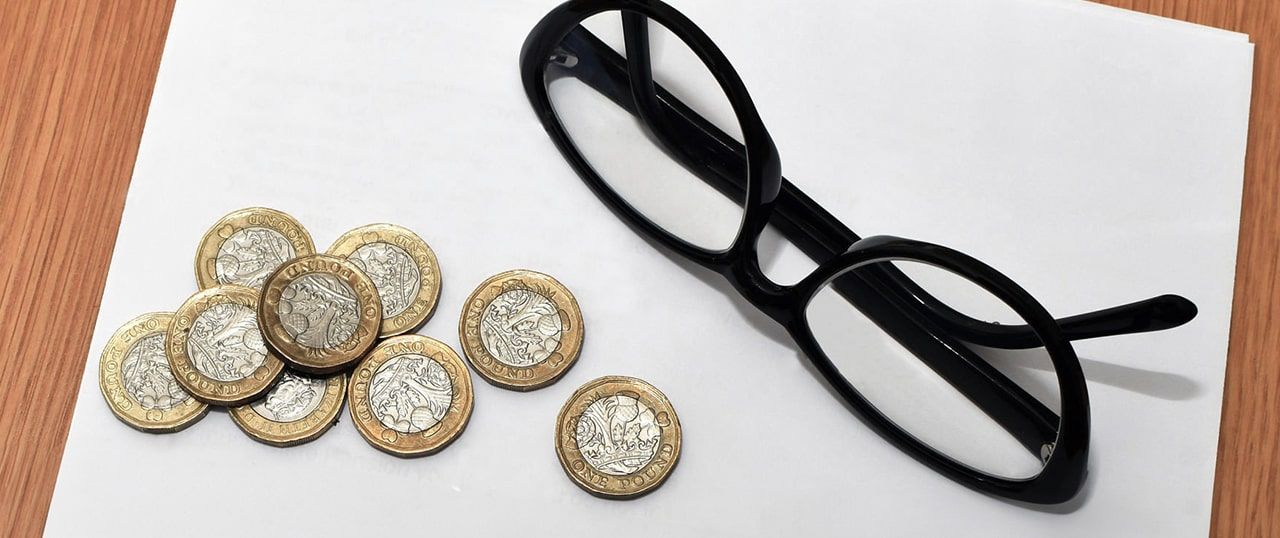
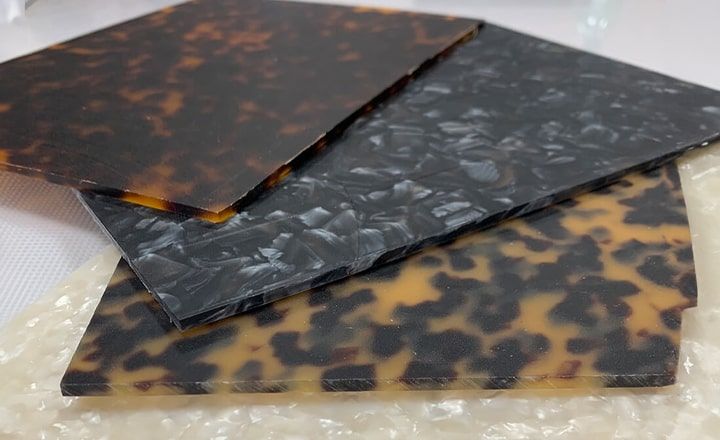
Glasses can be made of a variety of different materials, including but not limited to titanium, stainless steel, nickel silver, acetate and plastic. They can also be made of eco-friendly materials which are bio-based and recycled.
Acetate frames
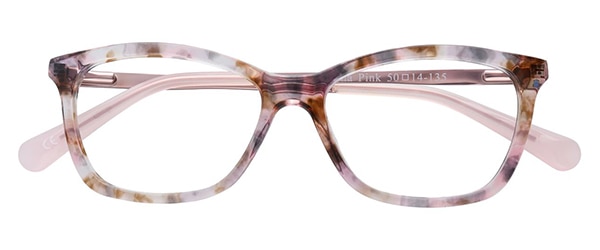
Acetate glasses are made from cellulose. This material is one of the most commonly used because of its versatile nature. It comes in a multitude of colours, patterns and designs. It can easily be moulded into various contemporary styles.
Plastic frames
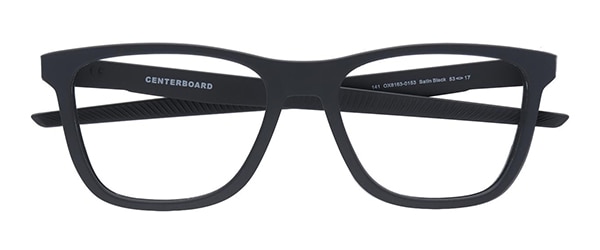
Plastic glasses are normally made from polyamide, nylon, carbon, SPX, or Optyl. These materials are affordable and sturdy. These kind of frames can take a little longer to adjust to because they do not tend to have metal wires in the temples like acetate frames. However, some plastics are eco-friendly and top brands like Oakley use their own innovative plastics. Their O-Matter™ material for example is a patented nylon composite that is highly durable and flexible.
Stainless steel frames
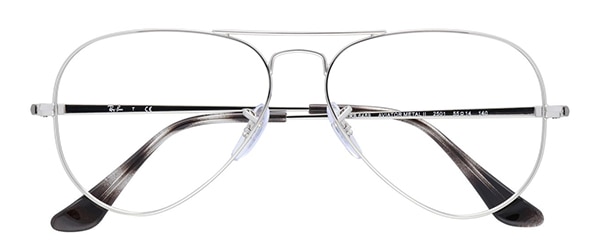
Stainless steel is a hard-wearing metal and a popular choice of material for glasses. The material is resistant to corrosion and lightweight. Metal frames also frequently include adjustable rubber nose pads for a more bespoke fit.
Titanium frames
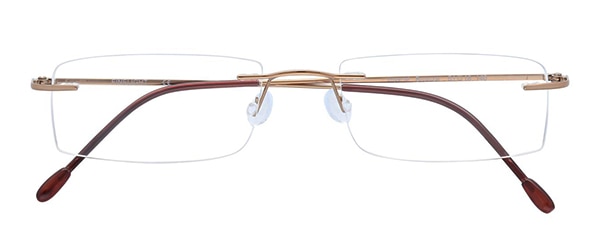
The wire cores (which are the parts that help retain the shape of the temples), hinges and other parts of glasses, as well as the frame itself sometimes, are very often made of sturdy titanium. This material is popular because not only is it strong, it is also remarkably lightweight. It is corrosion resistant and is also able to form unique shapes.
Carbon fibre frames
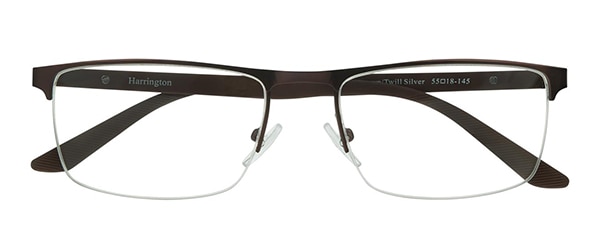
Reinforced carbon fibre is a contemporary material that is lightweight, sturdy and corrosion resistant. It requires complex manufacturing and may take some time to create.
Nylon fibre frames
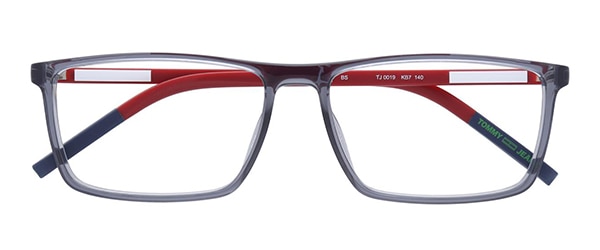
Commonly used for sports eyewear, nylon fibre is available in various colours, is flexible, easy to shape and resistant to heat and cold. Glasses using this material are also easy to make.
How are glasses made?
Glasses are made up of several components and therefore require a meticulous manufacturing process. It can take up to three weeks to turn a sheet of material into a finished frame.
The process involves several key steps. To create a pair of acetate frames, the production team first starts with a sheet of the material which they carefully sculpt into several parts, including the front of the frame and temples.
First of all, in order to create the front of the frame, the material is cut and shimmed to achieve the right thickness. Then, if needed, extra material is glued to specific areas of the design. It is then milled to remove any excess material. This helps to create the shape of the internal lens. The frame is then bent so that it is curved. Then the tumbling process begins, whereby the front of the frames are put into wooden barrels with coarse woods and pastes that, as the barrel rotates, gets rid of excess material and improves the overall finish. Next, the temples are cut and shaped from a slab of material. A wire core is inserted for added strength. The temples are then also tumbled before being connected to the front of the frame. The final design then goes through several rigorous final checks.
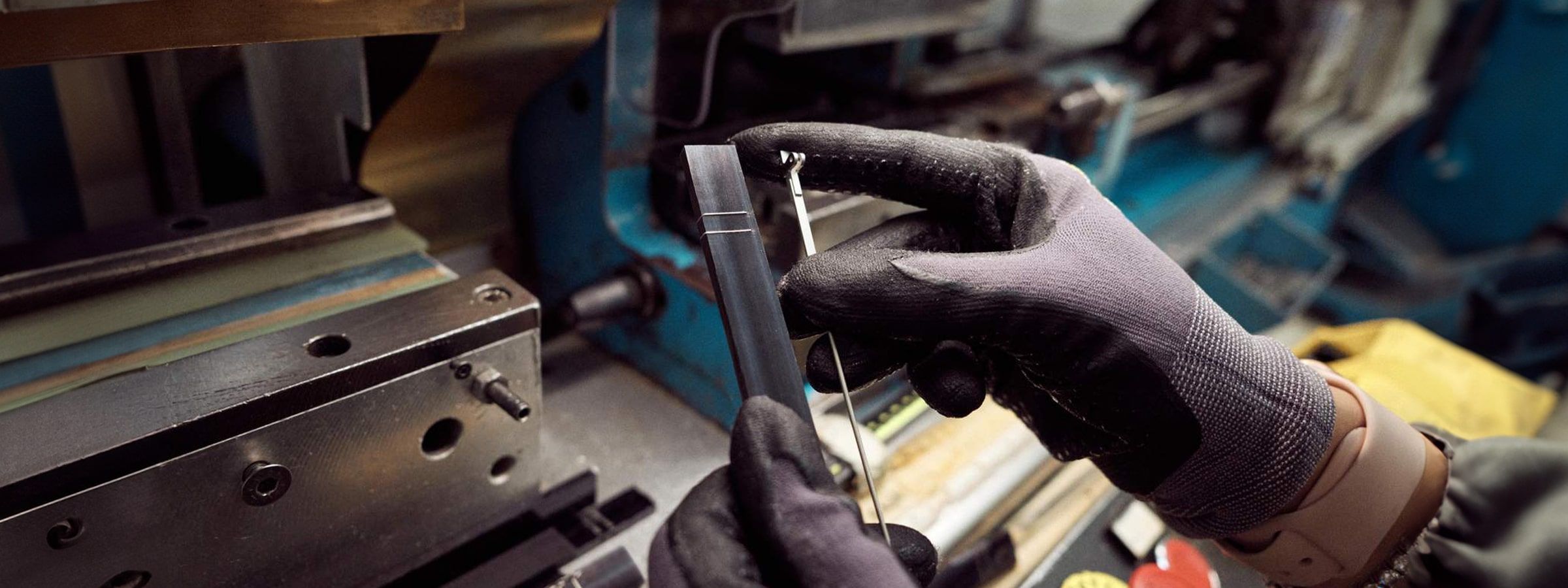
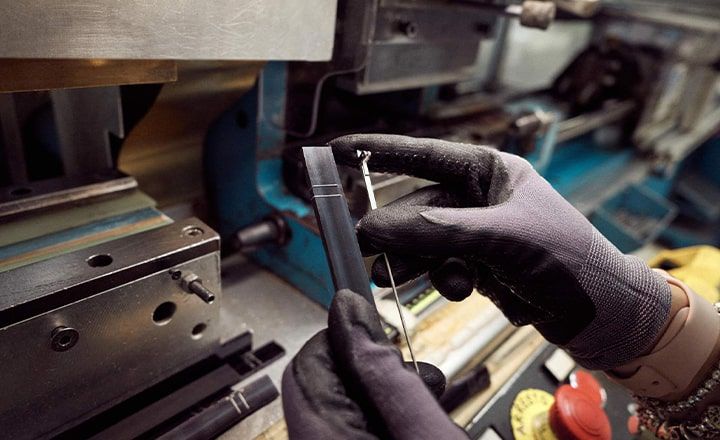
Metal frames, meanwhile, start with raw materials in the form of sheets, bars, or wires. To create the various components that will later make up a complete frame, the sheets of metal must first be cut. They are then stamped with the outline of the front of the frame before being carefully trimmed into shape and given a meticulous finish.
The metal bars are then processed which help to form essential components like the temples, hinges and fronts. The thickness of the bar is reduced using a process called turning. The bar is then bent and punched to achieve the desired shape.
Metal wire is mainly used to produce the rims (which support the lenses) of the metal frames. The coils are first unwound and then shaped accordingly using ‘hooping machines’.
All the components are put through a tumbling process at least once which helps to give them a smooth finish. They are polished and removed of any imperfections. The separate components are then connected together.
The manufacturing process requires a high level of quality control and precision – from machining and polishing to the putting together of components and the overall manual assembly.
Metal frames require an extensive range of surface treatments which help to enhance their aesthetic and ensure corrosion resistance.
What are glasses lenses made of?
There are a variety of different lens materials for your eyewear. Each type of lens material can assist in correcting refractive errors like short-sightedness, long-sightedness, astigmatism, or presbyopia.
Before finding out about the various lens materials, it is important to have an understanding of refractive index. Some materials are classified by the index of refraction, which specifies how quickly light travels through a specific material.
Put simply, the higher the refractive index, the more light is bent by the material, therefore less lens material is needed compared to a lens with a lower refractive index.
So essentially, for any eye prescription, the higher the refractive index the thinner the lens will be.
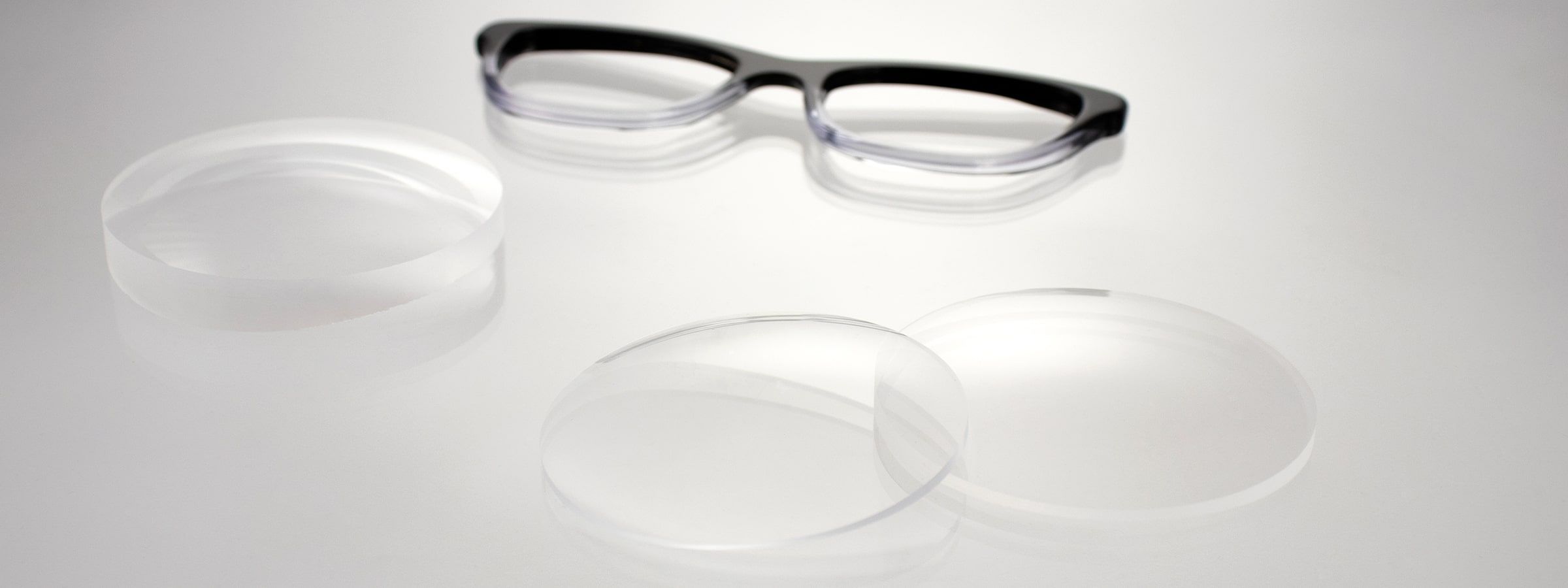
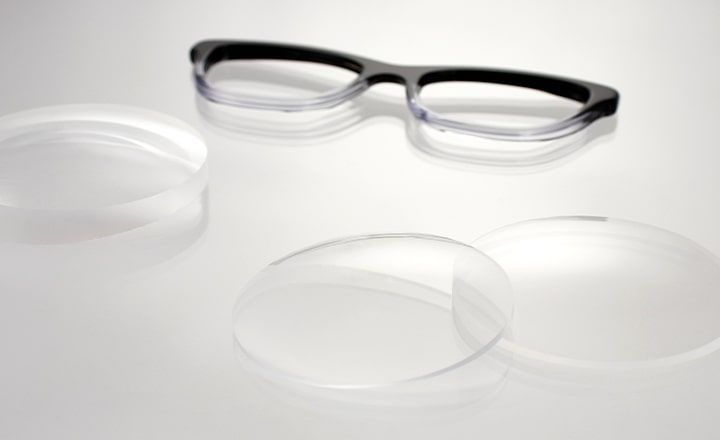
Types of lens materials
Lenses used to be made of glass but due to the fact they were uncomfortable, heavy and easily breakable, they have since been replaced by various plastic materials.
Glasses lenses are most commonly constructed from CR39 plastic which has excellent optical features. However, CR39 plastic lenses are often much thicker than other plastics due to the fact they have a low index of refraction of 1.5. This material is normally very affordable and recommended for people with lower prescriptions.
Polycarbonate is the most durable of the lens materials and therefore is ideal for sports lovers and those whose glasses are susceptible to damage. It comes with 100% UV protection and is normally recommended for rimless frames. Theses lenses have a refractive index of 1.59 which is great for people with a high prescription.
The mid-index plastic material at 1.6 is 20% thinner and lighter than low-index materials like CR39. It is suitable for medium power prescriptions.
A high-index plastic lens with a refractive index of 1.67 is around 33% thinner, whereas a lens with a refractive index of 1.74 will be around 42% thinner. They are best for people with a very strong prescription.
At Glasses Direct, we have a variety of lens packages suitable for different prescriptions which all come with a reliable scratch-resistant coating and depending on the package, anti-reflective and UV protection. You can easily find an option that best suits you and your requirements.
How are glasses lenses made?
The lenses for your glasses are made according to your prescription using a combination of technology, science and creativity. There are various prescriptions and frame sizes which means every lens has a different curvature.
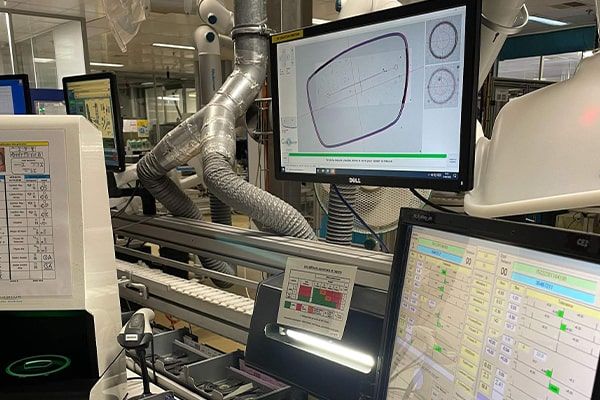
Step 1: Lens preparation
Once an optician has reviewed and authorised your order, a technician in the laboratory will enter the optical prescription for a pair of plastic lenses into a computer. The unique prescription is then inputted and any further information required to create the lenses is made accessible.
Step 2: Lens selection
It is then the role of the technician to select the correct plastic lens blanks for the prescription, using the information available. Each blank is then placed on a prescription tray with the frames and the customer's order.
The technician then marks the lens blanks at the optical centre using an instrument known as a lensometer. The centre point is the precise location that the customer will look through with their pupil and is the most transparent point of the lens.
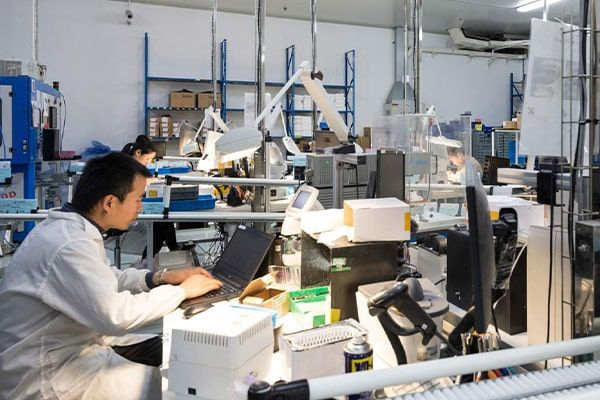
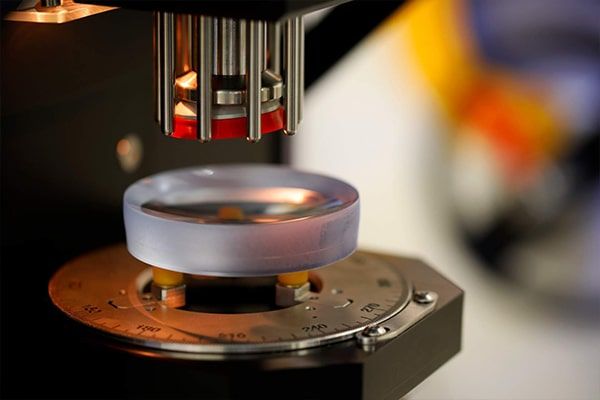
Step 3: Blocking
Next, we move onto the blocking stage of the process. Each lens is given a protective layer to prevent scratches during the procedure.
The lens is attached to the blocker machine using a heated lead alloy. The technician connects each lens blank one after the other. The lens is ground and polished by the machine.
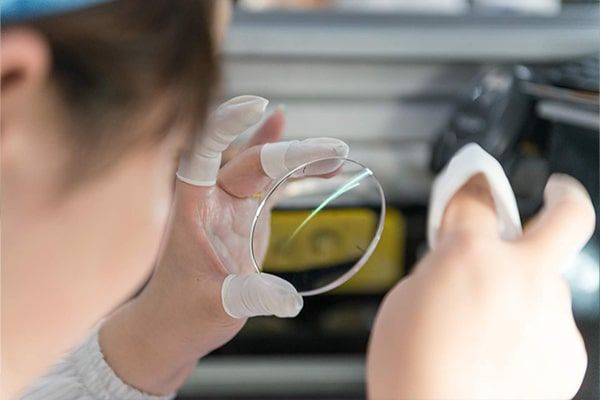
Step 5: Polishing
Once the back surface of the lens is ground into the desired shape, the surface of each lens is polished, bevelled and cleaned using a range of tools which includes a fining machine and soft sandpaper. It is important to note that this process does not alter the optical quality of the lens.
Step 6: De-blocking and cleaning
The blocks which are attached to each lens are carefully taken away using a small hammer and the tape is also manually removed. Following this, the lenses are sanitised with several chemicals and pure water to remove any remnants. The lenses are then dried off and prepared for the next stage.
The left and right lenses are labelled accordingly before being placed in the lensometer for final checks.
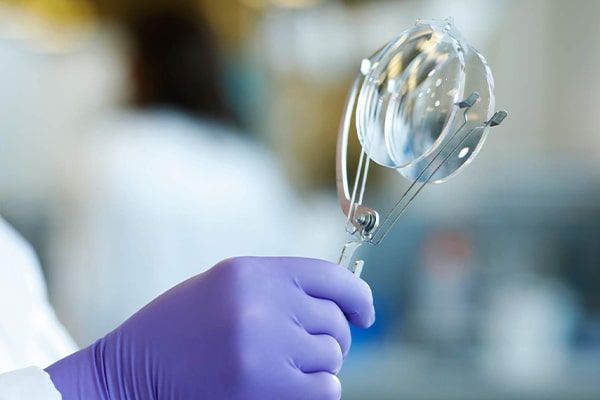
Step 8: Tints and coatings
As the very last and most technically challenging phase of the process, the lenses are dipped in UV treatment and given a tint if required. Prior to the dipping procedure, a hard coating will be applied to protect against any abrasions. At Glasses Direct, most sunglass tints come pre-tinted and will already have a UV coating applied.
The most common treatments for lenses include UV tints, scratch-resistant and light-adaptive coatings such as a photochromic coating which causes the lens to darken when exposed to UV light.
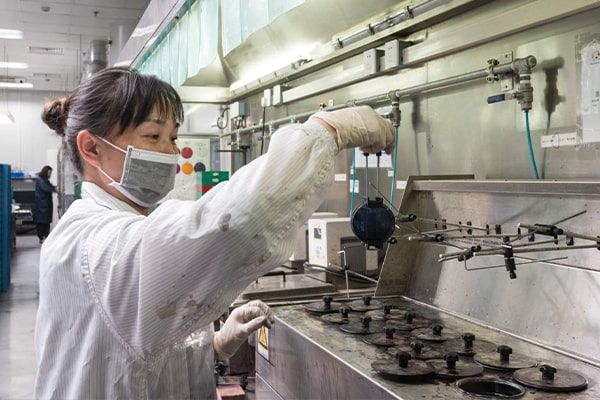
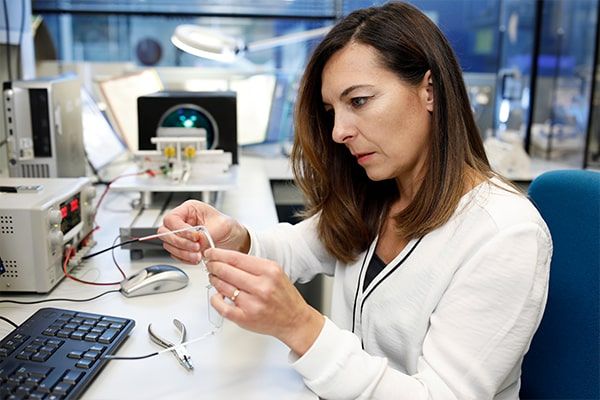
Step 9: Quality control and inspection
Each lens must be tested scrupulously to ensure it meets the necessary quality standards. They are first inspected visually to ensure there is no dust or damage. A mechanical inspection is also carried out to guarantee that each one is up to standard. The frames are also thoroughly inspected during this and finally cleaned. All frames are checked in the UK before being dispatched and delivered to your door.